Integrated Resin and Metal Molding Design for EV Motor Parts
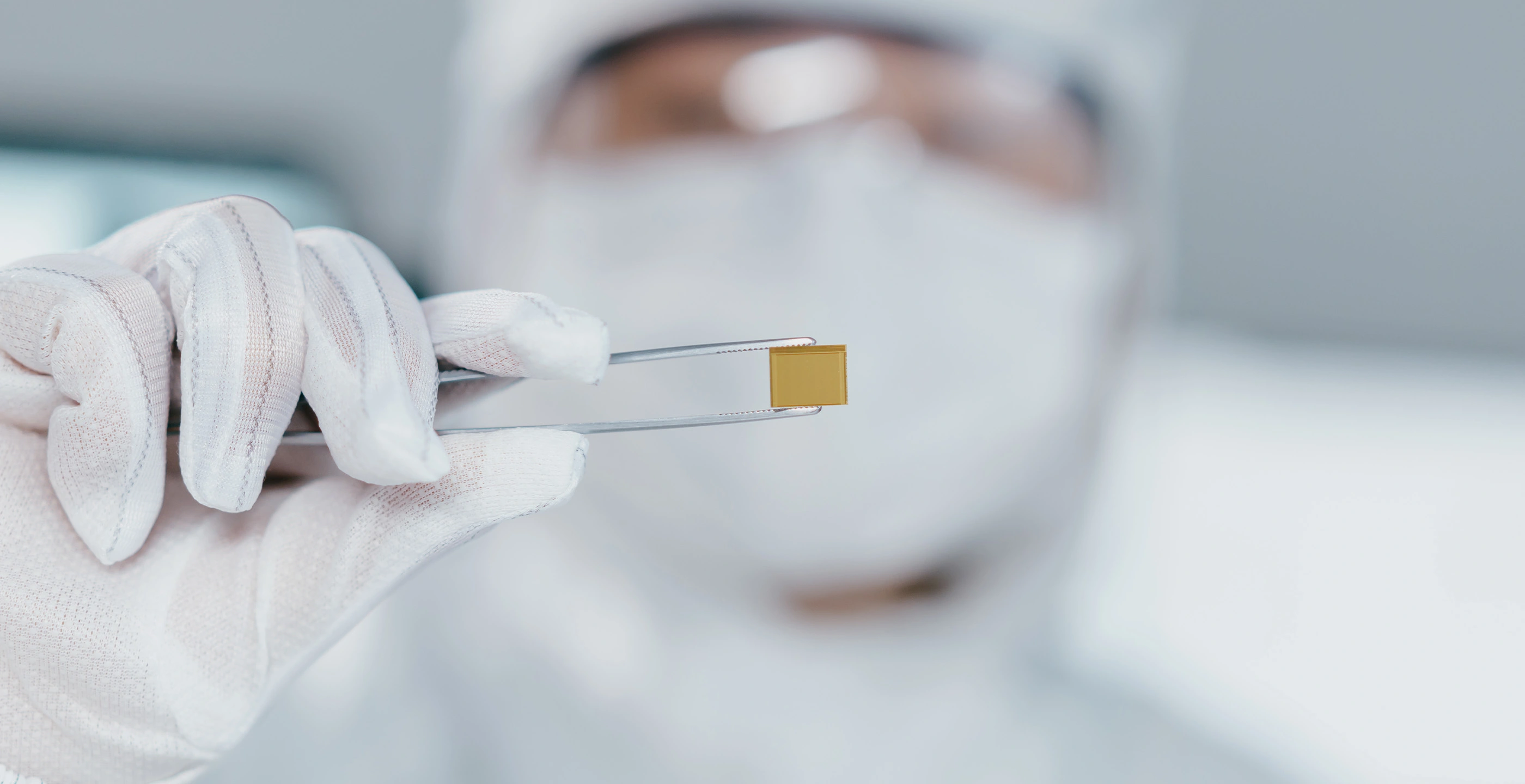
California’s recent legislative step to ban gas-powered cars by 2035 is just one of the bold moves paving the way for significant growth in the electric vehicle (EV) market. While it’s always been important, an efficient and effective system of mass production is now at the forefront of every EV company’s mind.
Manufacturers and engineers are striving to improve processes and systems to produce and assemble large quantities of high-quality, standardized auto parts and accessories. They are also looking for ways to improve the miniaturization of certain parts to help decrease weight and ultimately improve vehicle efficiency.
There are several vital components in EVs that could benefit from this kind of improved miniaturization and production, including the motor, battery, and on-board charger. One particular point of interest, however, is the inverter—the electronic device that makes the DC electricity from batteries usable by AC motors.
The inverter is a complicated piece of machinery that includes hundreds of small components made of various integrated materials, making them a challenge to build. NAGASE has been working in lockstep with manufacturers to address their needs and develop smart solutions to complex problems—like inverter assembly—that can hinder the flow of production.
The Customer Challenge: Dimensional Stability for Component Miniaturization
Modern EV design demands smaller and smaller motorized parts to make room for more vehicle systems as well as to reduce overall vehicle weight. However, the process of miniaturizing such parts is more complex than reducing mold sizes for the substrate, resin molding, and metal components individually.
When manufacturers produce small parts that comprise multiple components, they often run into two issues: postcontraction and differing coefficients of linear thermal expansion (CTE).
Postcontraction
After a liquid resin is injected into a mold to produce a component, it gradually shrinks over the next 48 hours as it cools. This phenomenon is called postcontraction. While it’s possible to account for the dimensional changes in the component, postcontraction can warp or bend components, which can cause future issues such as rattling and slipping. In some cases, a warped part won’t be able to be assembled and parts that crack or break from postcontraction won’t be usable at all.
Differing Coefficients of Linear Thermal Expansion
Manufacturers of parts that integrate different components must also account for the differing coefficients of linear thermal expansion (CTE). Most materials tend to change size when heated and cooled, but do so at different rates. Products such as bimetal thermometers take advantage of this principle, but for miniaturized parts, exposure to high or low temperatures can lead to cracks and breaks in the resin.
At the same time, automobile manufacturers expect miniaturized parts to pass a heat cycle test that exposes the parts to a temperature range between -40°C (-40°F) and 80°C (175°F) over 1,000 cycles.
Unless the resin in the part is of the right type, at the right thickness, and in the right position, a miniaturized part cannot survive postcontraction or pass the heat cycle test. This is what makes achieving acceptable dimensional stability a core challenge for manufacturers of miniaturized parts.
Our Solution: Unique Molds to Solve Unique Problems
NAGASE has developed a solution to help manufacturers of miniaturized, integrated parts.
To start, we began with the goal of creating a small and lightweight inverter for the auto industry, all on our end. Through a process of trial and error using our advanced technologies in resin and molding, we created and assembled all the many necessary parts into one complete streamlined unit.
This is a major win for manufacturers as we can use molding to efficiently produce an integrated part that includes both copper and resin—and even add other parts such as insulating films, magnetic cores, substrates, and press-fit pins. Oftentimes in similar applications, various small components must be assembled together and a component may be missed. This innovative process prevents cracking and warping of the different components and ensures the unit’s reliable performance. Moreover, since we can make each tiny part smaller through this method, the result is a further miniaturized, lighter-weight inverter. We also use materials strong enough to withstand postcontraction, and designed the part to be small enough to free up space for other components.
With this solution, we can solve several complex problems for manufacturers looking to replace outserting processes with insert molding. We remove the tedious work of tracking and assembling what can sometimes exceed a hundred tiny pieces. And we can handle the varying CTEs and forms of postcontraction that many component manufacturers struggle to overcome . Rather than accounting for these issues on their own, manufacturers can instead purchase a completed unit that adheres to their unique requirements and quality standards from NAGASE.
Making the Impossible Possible through Strategic Design
More than just a solution for inverters, our method for integrating components can be applied to various resin/metal composite parts found within the motors of electric vehicles.
Our team has extensive experience dealing with large-size, multi-point component inserts, and inserts of various components (substrates, cores, bus bars, and nuts). Common applications include batteries, in-vehicle chargers, and current sensors—all of which we create in collaboration with our customers, with exceptional quality and mass production in mind.
Another top priority, as demonstrated in the case of the inverter, is to minimize the risk of cracking and warpage. Through our strategic designs and proposals at the development stage, we make what customers think is impossible possible, preventing avoidable issues during thermal cycle tests and providing optimal arrangement and positioning of parts to enable proper molding.
Then, when design and testing are complete, we bring the end product to life through mass production and superior quality control efforts. We are ISO9001 certified, comply with all rules and regulations for stable manufacturing, and are dedicated to continuous improvement—we even train our entire staff on quality control practices to minimize any risk.
Unmatched Expertise & Technology
In addition to our design expertise and commitment to quality, what sets NAGASE apart is our extensive experience with chemicals, plastics, electronics, automotive, and life sciences. While other resin manufacturers have a narrow focus, we bring a wide breadth of knowledge and resources from across different industries. We also have several patents for resin insert molding, giving us a technological advantage over other producers of interior parts. This allows us to design and develop creative, cutting-edge solutions using a significant number of advanced technologies and specialized equipment.
To learn more about how NAGASE can make your manufacturing process easier or to present us with a challenge that you need support solving, contact one of our experts.
Related Resources
We’re Here to Help
Complete the following fields with your information, as well as a short, detailed description of your request and a NAGASE Specialist will be in touch with you shortly.