A Clear Winner: A Photoresist Success Story
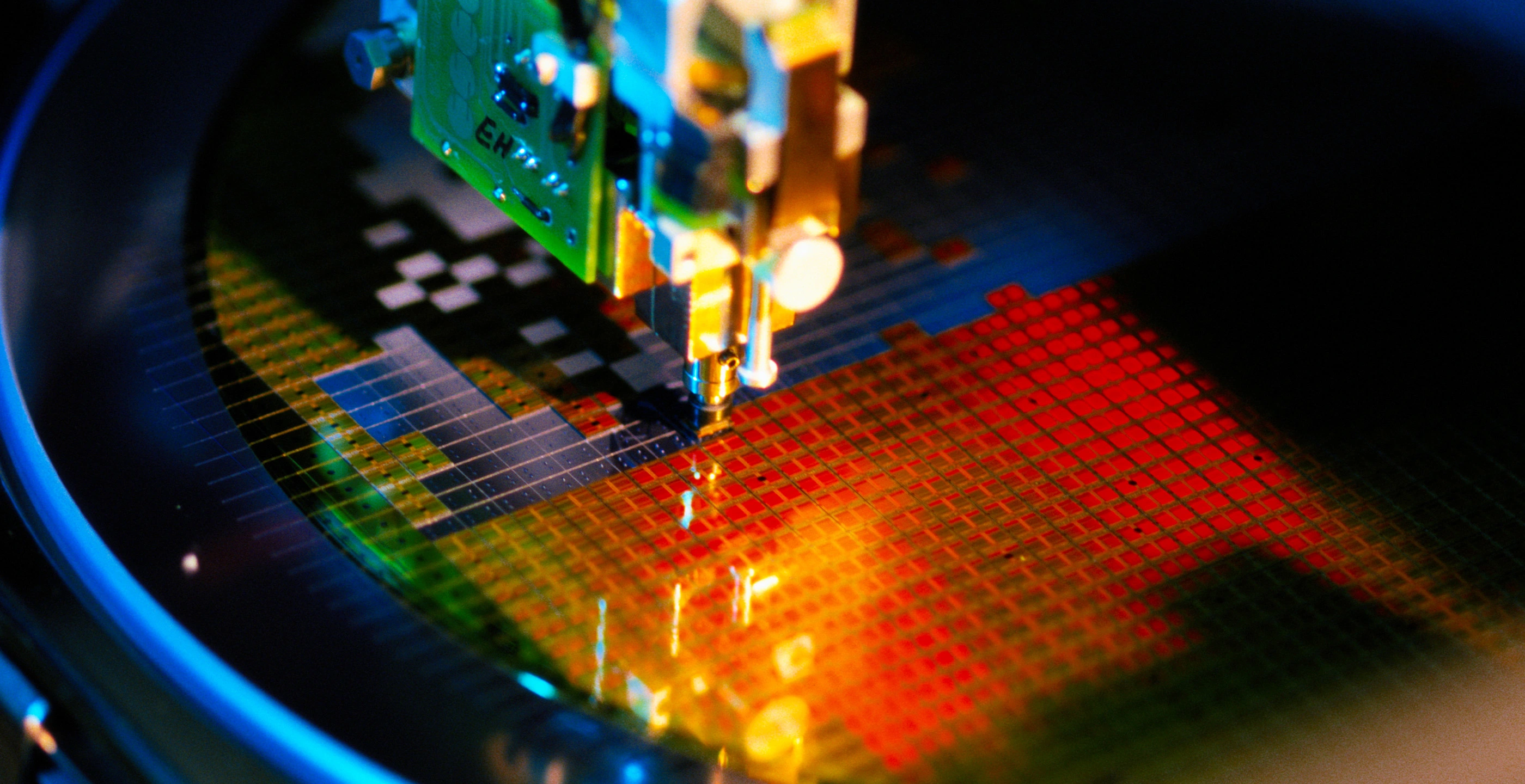
The photolithography process is one of the crucial elements in the electronics industry. The process uses a photoresist, which is a photosensitive material, and forms a patterned coating layer on a surface of the base material. This process, however, can result in damage to the base material used in the manufacturing process.
A device and electronic components manufacturer in the semiconductor industry, having experienced a metal wiring problem in their etching process, approached NAGASE. The customer believed that eliminating the etching process could prevent damage to the base material from chemicals such as strong acids and alkali used in the etching process. In general, the lift-off process is widely known as a method that removes the etching process. Customers have reported the following problems with the bi-layer process, one of the lift-off processes:
- Poor peelability or solubility of its own
- Limitations on available resist shapes
- The occurrence of intermixing the under-layer with the upper-layer materials
To address these problems, the customer had to increase the number of steps taken in the manufacturing process. Furthermore, they needed additional materials to fulfill these extra steps. The increase in time and materials added to operating costs, significantly reducing profit margins. Our customer was looking for a solution as they did not want to pass these extra costs to their customer base.
Testing, Evaluation & Collaboration Methodology
We collaborated with the customer to assess the situation and determined that we needed to focus on three key features:
- Adoption of a fine patterning technique
- Addressing a height difference
- Prevention of metal burrs (the formation of rough edges or ridges on the metal piece)
The customer emphasized the need for a resist with a unique shape suitable for making a hollow structure. Their goal was to reduce the required number of manufacturing processing hours as well as the number of materials used. They hoped to accomplish this by finding a patterning material that could eliminate the etching process.
The Nagase ChemteX team concluded that the customer would benefit from an advanced adhesive application. Thus, it developed a unique photoresist (photosensitive material) for the lift-off process. We accomplished this through a three-step action plan consisting of photoresist patterning, metal forming, and photoresist removal.
Survey & Analysis
NAGASE customized a series of the coating process and the fine-tuned the composition of the resist. Based on the results of its sample evaluation, it performed a plan-do-check-act (PDCA) cycle for further improvement of the product and formulation tuning. The result and answer to the customer’s issue was the development of the BLX Series, an under-material for the bi-layer lift-off process. One of the material’s many benefits is that it can be applied to various upper-layer resists without intermixing. Additionally, it adapts to various film thickness designs for the upper- and under-layers. Lastly, it is versatile, as the amount of side etching can be arbitrarily adjusted depending on the process conditions.
Hypothesis & Verification
The outcome was a success. The BLX Series solved the problem of performance and cost, which could not be satisfied by the underlayer material of the existing two-layer lift-off process. The ultimate result was that the BLX Series enabled the customer to shorten the manufacturing process and reduce the number of materials used. Those benefits significantly contributed to the customer’s bottom line and sustainability.
Conclusion
We at NAGASE thrive on solving unique and challenging issues faced by our customers. In this case, the customer, a device and electronic components manufacturer in the semiconductor industry, sought a special shape resist with high resolution. We realized that this customer would benefit from an advanced adhesive application. Thus, through a three-step action plan, we developed a unique photoresist (photosensitive material) for the lift-off process. By applying the BLX Series, the customer has lowered costs, increased sales, and measurably improved their bottom line.
Related Resources
We’re Here to Help
Complete the following fields with your information, as well as a short, detailed description of your request and a NAGASE Specialist will be in touch with you shortly.